汽车传动轴固定节是汽车驱动系统中一个重要的零部件,传动轴固定节的端面,如图1示。由于固定节中6粒钢球由工人手工进行安装,有可能发生少装的情况,如不及时发现,将出现质量问题,影响产品的正常使用和企业的声誉。因此根据厂方要求设计了此套系统,系统采用无损检测,运用图象处理与模式识别技术,对CCD拍摄到的图象进行处理,作出漏装与不漏装判断,并对漏装工件进行声光报警。
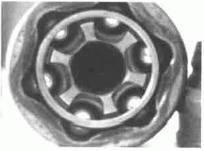
图1 汽车传动轴固定节端面
一、系统组成与控制过程
1. 系统组成
系统主要由机械部分、电气部分、控制部分组成。机械部分主要是完成零件的传送(从安装位置到检测位置,再送到下一个工序的加工位置)、定位(保证零件与摄像头的同心度)以及不合格零件的剔除;电气部分有传感器、汽缸等执行机构组成;控制部分采用PLC和工控机集成控制。系统硬件配置主要有工控机、可编程控制器、CCD摄像头、图像采集卡、I/O接口板、传感器等硬件及部分外围电路组成,它们的结构,如图2示。
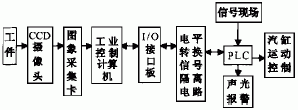
图2 系统组成图
2. 控制流程
系统由工控机作为上位机,PLC作为下位机。系统的自动控制流程为:
- 工控机与PLC进行通信握手,表明一切就绪;
- 送料位置传感器检测到工件,发信号给PLC;
- PLC根据测量位置传感器状态判断测量位置是否有工件;
- 如果测量位置没有工件,则PLC发信号驱动汽缸,放开送料挡块;
- 测量位置传感器检测到工件已经到达,发信号给PLC;
- PLC进行延时,目的是让工件稳定有利于拍摄,然后发信号给工控机并延时,目的是让计算机进行图象处理与模式识别;
- 工控机执行程序由CCD摄像头摄取图像,由工控机实时处理图像,作出漏装或非漏装判断结果。把结果发给PLC;
- PLC判断结果信息,如果全装且翻转位置无工件,发信号驱动汽缸放开定位挡块;如果漏装,PLC发信号驱动报警灯和蜂鸣器,进行声光报警由工人手工剔除。
- PLC判断下料槽是否可以下料,若可以则翻转工件进入下一道工序。重复顺序执行2~8,就达到了系统的自动检测。从执行过程中可以看到,前后两个位置都实现了互锁。系统控制流程,如图3示。
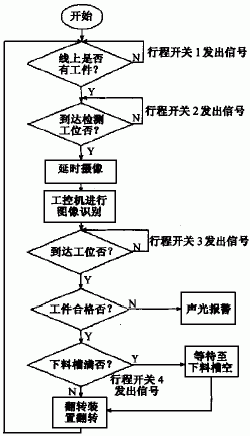
图3 系统流程
在这个系统中,实现了工控机与PLC的集成控制。工控机主要完成对图象的处理,PLC完成对现场控制信号的采集与执行元件的驱动,它们之间的通信采用I/O卡来实现。控制系统物理结构,如图4示。
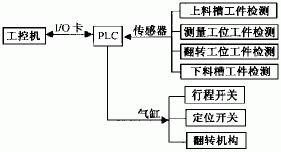
图4 控制系统物理结构
二、系统硬件模块
系统硬件模块主要分为数据采集子系统,微机基本子系统,数据分配子系统及基本I/O系统。它们之间的结构,如图5示。
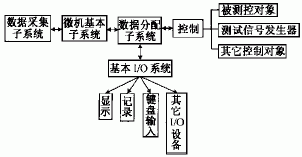
图5 硬件结构组成
1. 微机基本子系统
它是整个系统的核心,对整个系统起监督、管理、控制作用,例如进行复杂的信号处理、控制决策、产生特殊的测试信号,控制整个检测过程等等。同时,利用微机强大的信息处理能力和高速运算能力,实现命令识别、逻辑判断、图像处理、系统动态特性的自校正、系统自适应等功能。
2. 数据采集子系统
用于和传感器、检测元件联接,实现图像数据的采集、整理并经接口传送到微机子系统处理。
3. 数据分配子系统
实现对被测工件、测试信号发生器以及检测操作过程的自动控制。
4. 基本I/O子系统
用于实现人机对话、输入或改变系统参数、改变系统工作状态、输出检测结果、动态显示测控过程、发出报警信号等。
三、系统软件设计
软件设计采用模块化和结构化的程序设计方法,即自顶向下、逐步求精的设计方法,并且适当划分模块以提高设计与调试的效率。该系统不但要接受来自传感器、待测工件的信号,还要接受和处理来自于控制面板的按钮信号,以及由图像采集卡传来的数字信号,而且要求系统具有实时处理能力。因此,系统软件对实时性有一定的要求,同时还要对系统资源进行管理和调度。
1. 上位机软件设计
上位机监控软件主要由数据采集程序、检测与控制算法程序、中断服务程序、故障自诊断与处理程序等组成。系统模块划分如下:
(1) 初始化模块
对系统中各硬件资源设定明确的初始化状态,包括对可编程器件初始化,各I/O口初始状态设定,为系统硬件资源分配任务等。
包括堆栈初始化、状态变量初始化、各软件标志初始化、各变量存储单元初始化、系统参数初始化等。
(2) 数据采集模块
控制摄像头摄取图像,通过图像采集卡完成A/D转换,并生成待处理的数据文件。
(3) 检测/控制模块
对得到的图像数据文件进行分析、计算、比较、检测,判别工件是否合格,并实现对键盘的管理。
(4) 中断管理模块
针对系统中的各种中断源和所选用的微处理机的中断结构,设计相应的中断处理程序模块,包括中断管理模块和中断服务模块。
(5) 显示管理模块
用于实时更新显示图像和数据,并对报警指示灯进行管理。
(6) 时钟管理模块
包括数据采样周期定时、控制周期定时、动态刷新周期定时、及故障监视电路的定时信号等。
(7) 故障自诊断与处理模块
它是提高系统的可靠性和可维护性的重要手段,主要采取开机自检的形式,每当电源接通或复位后,系统自动执行一次自检程序,对硬件电路进行一次检测。上位机监控软件主要程序流程,如图6所示。
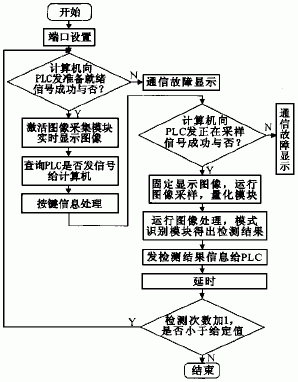
图6 上位机监控程序框图
2. PLC软件设计
PLC的程序采用了模块化设计方法,由主程序、手动控制程序、故障处理程序等模块构成。根据系统要求,PLC的I/O分配,如表1示。
(1) 输入输出信号
表1 PLC输入输出信号
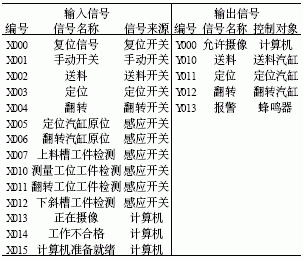
(2) 梯形图编制
根据控制过程及输入输出信号编制出梯形图。PLC采用循环扫描方式,按梯形图从上而下,从左而右的先后顺序予以执行。同时,前后两个工件位置都进行互锁。部分梯形图,如图7示。
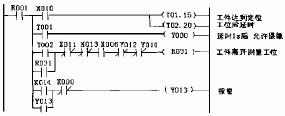
图7 定位工位梯形图
R001是内部继电器,表示选择“自动”,当PLC得到信号X010时,即传感器检测到定位工位有工件时,延时并输出允许摄像信号Y000,然后再延时2s(等待计算机作出判断)并且当翻转汽缸不在原位和翻转工位无工件时,输出工件可以离开定位工位信号。如果PLC接到计算机发出的“工件不合格”信号,即X014后,报警,直到按复位键停止报警。
四、计算机与PLC的通信
在计算机与PLC的集成控制系统中,一个关键的技术问题是计算机与PLC的通信问题。在本课题中,对于计算机与PLC之间的通信,我们考虑了两种实现方法:一种是利用串口通信,另外可通过I/O卡来实现。由于串口通信在实时性、可靠性、抗干扰性等方面都没有I/O卡好,又根据厂里具体情况,最后还是选用了后一种方法。I/O卡即开关量输入输出卡,在此项目中,我们选择了PCL—724,24位数字I/O卡,传输速率为300KB/s。该I/O卡具有2个八位端口(A,B),端口地址范围为200H~3FFH,两端口都可以进行输入输出操作,在进行输入输出操作时,无需进行握手,因为数据可以直接写或读到设定的端口。由PLC输入输出信号表可以看到,PLC需要接收计算机3个信号,计算机需要接收PLC一个信号。它们的通信协议定义与地址设定,如表2示。
表2 计算机与PLC的通讯协议定义与地址表
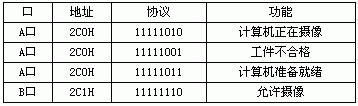
五、结束语
本系统是PLC与工控机集成控制的很好应用,投入运行后,为企业带来了可观的经济效益和社会效益。该系统在工业现场控制方面,尤其在PLC控制方面,以其卓越的控制功能和良好的性能价格比,赢得了用户的广泛赞誉。
马杏军,刘谨,陈敏贤